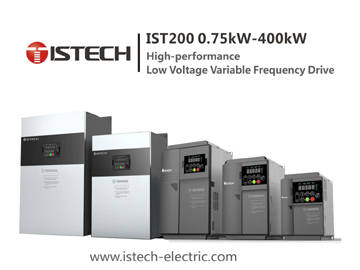
Input voltage: 1Phase 220V, 3Phase 220V,380V,480V
Adaptable Motor:
1Phase 220V 0.75kW-5.5kW 1hp-7.5hp
3Phase 220V 0.75kW-75kW 1hp-90hp
3Phase 380V 0.75kW-400kW 1hp-450hp
3Phase 480V 0.75kW-400kW 1hp-450hp
Control Mode: Vector Control(SVC,FVC),V/f
Start Torque:G type:0.5Hz 150%(SVC);0Hz 180%(FVC)
Items |
Specifications |
||
Control | Max. frequency | Vector control: 0~300 Hz; V/F control: 0~3200 Hz | |
Carrier frequency | 0.5~16 kHz | ||
Input frequency resolution |
Digital setting: 0.01 Hz; Analog setting: max. frequency x 0.025% |
||
Control mode | Sensorless vector control (SVC); Flux vector control (FVC); Voltage/Frequency (V/F) control | ||
Startup torque |
G type: 0.5Hz/150% (SVC); 0Hz/180% (FVC) P type: 0.5Hz/100% |
||
Speed range | 1:100 (SVC) | 1:1000 (FVC) | |
Speed stability precision | ±0.5%(SVC) | ±0.02%(FVC) | |
Torque control precision | ±5%(FVC) | ||
Overload capacity |
G type: 60s for 150% rated current, 3s for 180% rated current P type: 60s for 120% rated current, 3s for 150% rated current |
||
Torque boost | Fixed boost; Customized boost 0.1%~30.0% | ||
V/F Curve |
Straight-line V/F curve
Multi-point V/F curve N-power V/F curve (1.2-power, 1.4-power, 1.6-power, 1.8-power, square) |
||
V/F Separation | Complete separation; Half separation | ||
Ramp mode | Straight-line ramp; S-curve rampFour kinds of acceleration/deceleration time with the range of 0.0~6500.0s | ||
Operation | Running command Source | Operation panel; Control terminals; Serial communication port | |
Frequency source | Total 10 types, such as digital Setting; analog voltage setting; analog current setting; pulse setting and serial communication port setting | ||
Auxiliary frequency Source | Total 10 types. It can implement fine tuning of auxiliary frequency and frequency synthesis. | ||
Input terminal |
Standard: 5 digital input (DI)
1 supports up to 100 kHz high-speed pulse input; 2 analog input(AI); 1 only supports 0~10V voltage input; 1 supports 0~10V voltage input or 4~20mA current input. Expanding capacity: 5 DI 1 AI supports -10~10V voltage input and also supports PT100\PT1000 |
||
Output terminal |
Standard:
1 high-speed pulse output (open-collector) that supports 0–100 kHz square wave signal output; 1 digital output(DO); 1 relay output; 1 analog output(AO) that supports 0~20mA current output or 0~10 V voltage output Expanding capacity: 1 DO; 1 relay output; 1 AO supports 0~2mA current output or 0~10 V voltage output |
||
Display &
Operation Panel |
LED display | It displays the parameters. | |
Key locking and function selection | It can lock the keys partially or completely and define the function range of some keys so as to prevent mistake operation. | ||
Protection mode | Motor short-circuit detection at power-on, input/output phase loss protection, over current protection, overvoltage protection | ||
Environment |
Installation location | Indoor, free from direct sunlight, dust, corrosive gas,combustible gas, oil smoke, vapour, drip or salt. | |
Altitude | Lower than 1000 m | ||
Ambient temperature | -10℃~+40℃ | ||
Humidity | Less than 95%RH, without condensing | ||
Vibration | Less than 5.9 m/s2 (0.6 g) | ||
Storage temperature | -20℃~+60℃ |
Instantaneous power stop | When the power supply instantaneous stop, the load can feedback energy to compensates the voltage reduction, ensure the LV VFD can continuous operation for a short time. |
Virtual I/O | Five groups of virtual DI/Do can realize simple logic control. |
Timing control | Setting time range: 0.0min.~ 6500.0min. |
Multi-motor switchover | Four motors can be switched over via four groups of motor parameters. |
Multiple communicationprotocols | It supports 3 types communication via RS-485, Profibus-DP, CAN. |
Motor overheatprotection |
The optional I/O extension card enables AI3 to receive the motor temperature sensor input. |
Multiple encoder types | It supports various encoders such as differential encoder, open-collector encoder, resolver and UVW encoder. |
Overvoltage / Over current stall control | The current and voltage are limited automatically during the running process so as to avoid frequent tripping due to overvoltage/overcurrent. |
Rapid current limit | It helps to avoid frequent over current faults of the AC drive. |
Torque limit and control | It can limit the torque automatically and prevent frequent over current tripping during the running process. Torque control can be implemented in the FVC mode. |
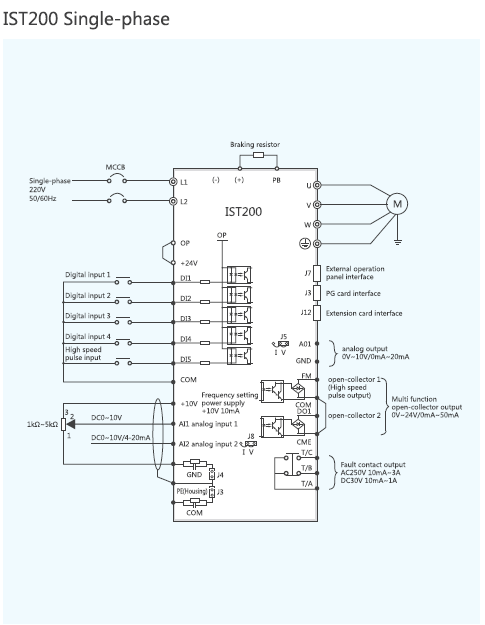
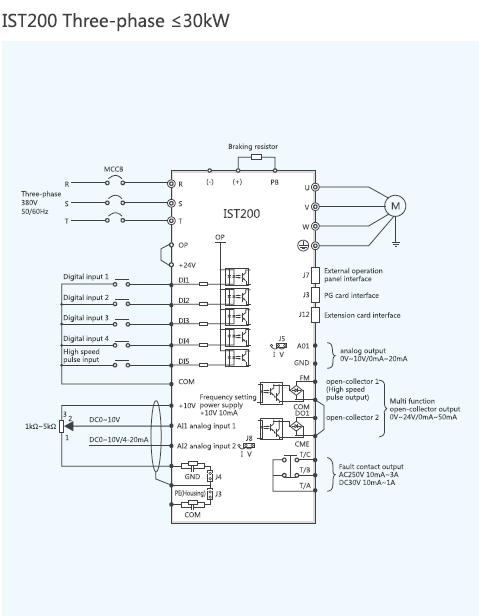
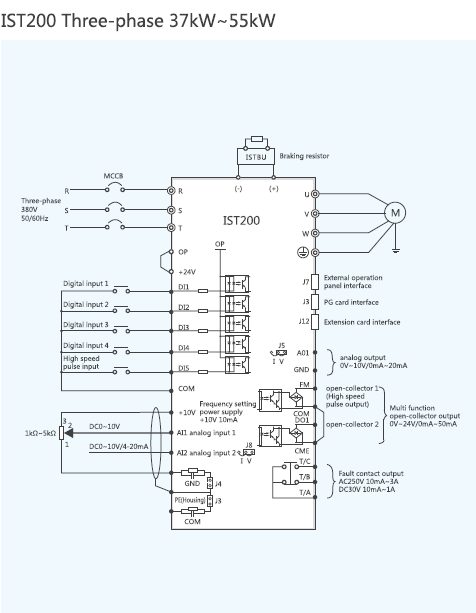
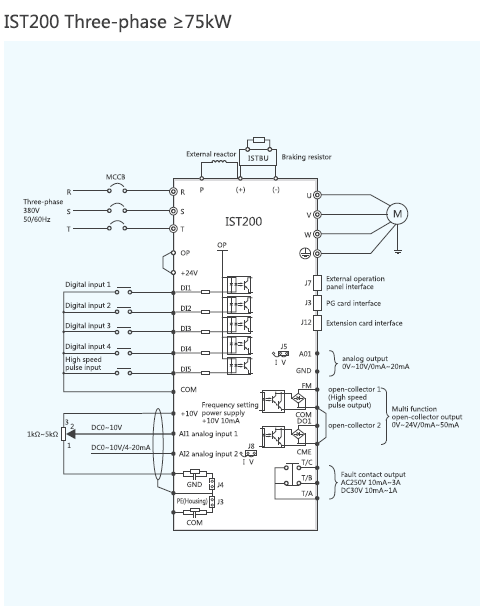